When Jake Sanchez and his colleagues at Formlabs developed the first iteration of the company’s new 3D printer, Form 4, it almost looked like an example of Brutalist architecture; one that Sanchez believed could rival Boston’s historic City Hall.
But, of course, the first iteration was just the beginning of a long development journey that Sanchez and his teammates traversed to transform those inauspicious beginnings into the polished, thoughtfully designed product that ultimately launched in April of this year.
Several iterations later — with a significantly redesigned form factor — the Form 4 team started to envision the product in its final state, as something that could really change the way professionals make physical products.
“That was the ‘aha moment’ for me, when I could suddenly picture this printer on my own desk as a product and not a project,” he said.
With so much inherent complexity, the development of Form 4 was a multifaceted, companywide undertaking. According to Product Lead Kyle McNulty, the 3D printer was launched along with 14 other consumable, accessory and material products, creating a complete, next-generation solution.
“It was our largest product development effort ever and involved every single person in our stereolithography research and development teams,” he said.
While cross-functional collaboration was key to the success of Form 4, so was a cutting-edge tech stack. Sanchez said tools like the Mazak vertical machining center and Omax waterjet were critical during the development phase, lending the product its myriad of capabilities.
Form 4 is more than an impactful new addition to the company’s product suite. Product Marketing Manager Elena Austras added that it’s helping the organization fulfill its mission to “build the tools that make it possible for anyone to bring their ideas to life.”
“We’re introducing a tool that is fast, versatile, reliable, accurate, intuitive and affordable, enabling our customers to unlock ideas and solve problems in ways that were not possible before,” she said.
ABOUT FORMLABS
Established by three MIT graduate students in 2011, Formlabs offers products and services that enable 3D printing capabilities for organizations across a wide range of industries, from manufacturing to medicine.
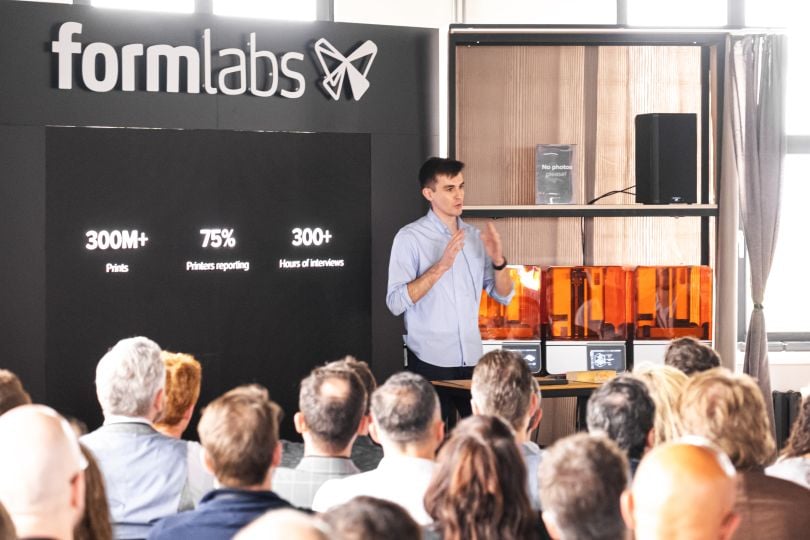
The Art of ‘Avoiding the Status Quo’
Although Austras has led eight multiproduct launches since joining Formlabs, the process that went into building Form 4 was unlike anything she had experienced before.
“Avoiding the status quo was imperative,” she said. “We recognized that operating ‘business as usual’ was inadequate, given the unparalleled scale and significance of this launch.”
“Avoiding the status quo was imperative.”
This mindset inspired Austras to form and lead a “Go-To-Market Cabinet,” which ensured teams outside of research and development operated in unison across the globe throughout the project. The group included representatives from 15 different functional teams involved in the launch process. The group met weekly to discuss workstream updates and blockers and ensure everyone was on the same page, all the way from planning to execution.
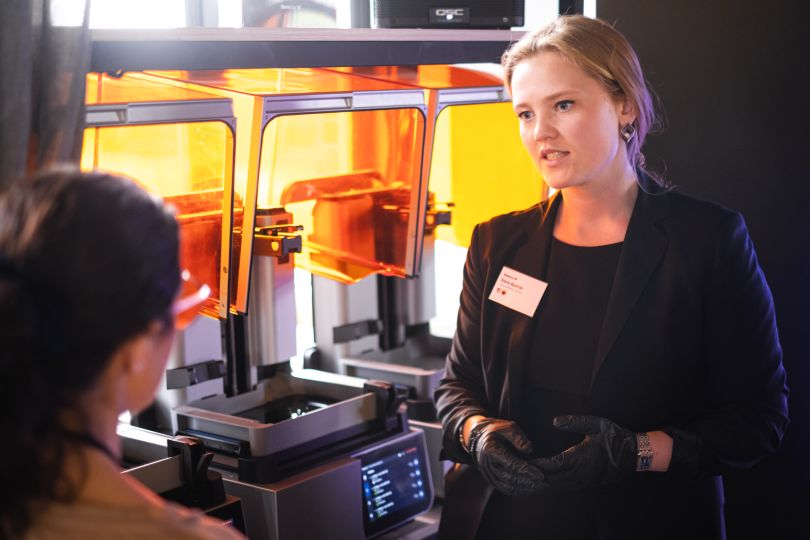
On the mechanical engineering side, team members were able to collaborate effectively under Sanchez’s guidance. Working together, Sanchez explained, they created Low Force Display technology, which they combined with the rest of the company’s existing subsystems, resulting in a product that produces more detailed, accurate parts three to four times faster than the organization’s other SLA machines.
Various tools were used to bring this complex architecture to life, including computer-aided design software Onshape, which engineers used to perfect their mechanical design. Sanchez said they used many other technologies to build, analyze and test their prototypes, including Keyence optical measuring equipment and an in-house optics lab, which allowed them to perform prototype production of their own light processing unit internally.
And according to Sanchez, designing the LPU and backlight unit was a feat unto itself, taking him and his peers on a “journey of discovery.” He explained that LCD screens are made by only a handful of vendors using advanced lithographic processes, and understanding the arcane details of the manufacture and structure of these screens was key to engineering them for peak performance, which would set their LPU apart from the competition. In the end, the company’s engineers were able to present an LPU with serious optical power and robustness.
As Sanchez and his peers built Form 4’s technological backbone, they relied on the company’s hardware groups, including optics, electrical engineering, industrial design and firmware. He shared that, while they leveraged a product requirements document and used tracking tools like Jira to collaborate, their greatest source of progress came from crowding around a physical whiteboard, even if that required some international travel.
“Engineering drawings aren’t enough to close the knowledge gap between the designers and the factory, so we sent engineers around the world to collaborate with our partners abroad,” Sanchez said. “While Zoom and similar tools are helpful, there’s no substitute for having boots on the ground when there are so many details to get right.”

THE PRODUCT PRO’S PERSPECTIVE
During any product development process, including the one that brought Form 4 to life, McNulty and his peers focus on one main responsibility: deliver the best product possible for customers that will drive meaningful business growth. But first, McNulty explained, they must focus on researching and synthesizing market and customer needs into actionable product and commercial requirements before tackling the task of cross-functional teamwork. “We work alongside engineering to make tradeoffs that always occur when building something; tradeoffs between cost, reliability, speed, print quality, timeline and more,” he explained.
Free to Fuel Progress
It can be hard to get details right when developing any product, let alone a product as intricate as Form 4.
But with the right caliber of teamwork, tools and expertise, technologists at Formlabs have the opportunity to fuel progress — and grow at the same time. For Austras, the greatest part of building Form 4 wasn’t simply seeing the finished product; it was the skills she strengthened throughout the process.
“I honed my strategic planning and execution skills, developed a deeper understanding of customer needs and refined my ability to lead cross-functional teams effectively,” she said.
As Austras learned how to adapt and stay agile amid challenges, she discovered the invaluable role each team member plays in bringing a new product to life. In her mind, every single individual helped shape the success of Form 4’s launch.
“Every single individual helped shape the success of Form 4’s launch.”
According to Sanchez, this emphasis on empowerment defines the company’s tech culture, extending beyond the creation of Form 4. Engineers in particular have ample opportunities to be fully involved in the product development process, as they’re able to follow their subsystems from whiteboard sketch to launch day, which ultimately leads to more effective solutions.
“This grants us a tremendous breadth of knowledge about how different parts of the product development cycle affect and are affected by our design decisions,” Sanchez said.
In his mind, autonomy defines the daily grind for Formlabs’ technologists. Everyone has the opportunity to leverage their unique talents and knowledge to help build a more innovative world — one 3D-printed model at a time.
“There’s no such thing as being a small cog in a giant machine here,” Sanchez said.